AS9100 certification is widely recognized and commonly required by aerospace and defense OEMs, military agencies, and contractors as a condition of supply. This application note identifies critical compliance challenges faced by manufacturers and demonstrates how Vision Engineering’s optical and measurement solutions directly address these pain points through enhanced inspection accuracy, measurement traceability, and ergonomic design to reduce human error.
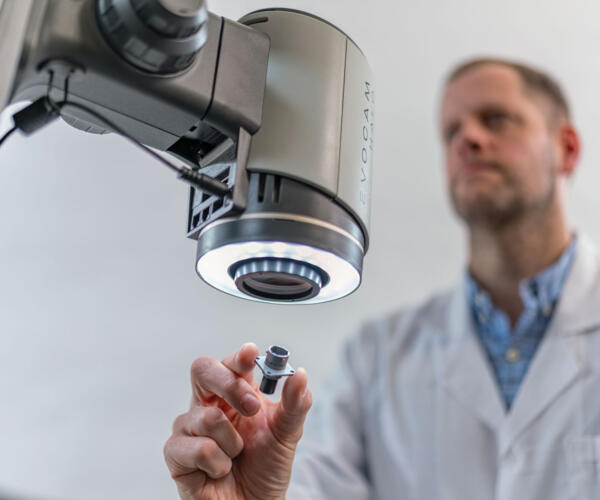
Introduction
The aerospace and defense industry operates under zero-defect expectations, where component failure can have catastrophic consequences. AS9100, the internationally recognized quality management system for aerospace, extends ISO 9001 requirements to address industry-specific needs, including product safety, risk management, configuration control, and comprehensive traceability. Manufacturers can face significant challenges in meeting these stringent requirements while maintaining operational efficiency.
Critical AS9100 Compliance Pain Points
1. Product Conformity and Defect Prevention Challenges
Manufacturers struggle with multiple inspection-related challenges that may threaten AS9100 compliance. Microscopic defect detection presents a fundamental challenge, as traditional inspection methods often miss surface defects that can lead to catastrophic failures. The identification of Foreign Object Debris (FOD) requires exceptional visual clarity that standard equipment lacks, creating significant quality risks. Complex assembly verification adds another layer of difficulty, as detecting misalignments and assembly errors in intricate components demands superior depth perception that conventional tools may not provide. Additionally, documentation requirements for capturing and documenting defects for Non-Conformance Reports (NCRs) may create workflow bottlenecks that impact productivity.
2. Measurement Traceability and Documentation Challenges
AS9100’s stringent traceability requirements create significant operational hurdles throughout the manufacturing process. Audit trail complexity requires maintaining comprehensive measurement documentation for every component inspected, creating a substantial administrative burden. Repeatability issues emerge when trying to ensure consistent measurements across different operators, shifts, and production runs, potentially compromising quality standards. Report generation becomes a critical bottleneck when creating compliant inspection reports quickly enough to maintain production flow. Calibration documentation presents ongoing challenges in demonstrating measurement accuracy and calibration status to demanding auditors. Furthermore, data management requirements for organizing and retrieving historical measurement data for customer or regulatory inquiries can overwhelm traditional quality systems.
3. Human Factors and Error Reduction Challenges
The human element presents critical quality risks that AS9100 specifically addresses through its requirements. Inspector fatigue from extended inspection sessions leads to decreased accuracy and missed defects, directly impacting product quality. Traditional microscopes cause ergonomic injuries including neck strain, eye fatigue, and repetitive stress injuries, affecting inspector performance and wellbeing. Inconsistent results arise from variations in operator skill levels and experience, as well as user discomfort and fatigue that create variability in inspection outcomes. Productivity loss due to physical discomfort reduces inspection throughput and efficiency, impacting overall manufacturing performance. Training complexity increases with difficult-to-use equipment and varying skill levels, leading to increased training time and operator errors. The turnover impact of ergonomic issues contributes to inspector turnover, affecting consistency and expertise within the quality team.
How Vision Engineering Systems Addresses Major AS9100 Challenges
1. Advanced Product Conformity and Defect Prevention Solutions
Vision Engineering’s high-resolution inspection systems provide comprehensive solutions to defect detection challenges through advanced optical and digital technologies.
High-Resolution Visual Inspection Systems
Stereo inspection systems deliver exceptional 3D depth perception for identifying surface defects and assembly errors that traditional inspection methods might miss. They provide enhanced visual clarity for detailed component inspection, ensuring that even the smallest anomalies are detected. The systems enable real-time, high-resolution imaging for immediate defect detection, allowing operators to identify and address issues as they occur. Image capture capabilities facilitate digital documentation and quick NCR attachment, streamlining the quality documentation process.
These systems facilitate early-stage identification of surface defects and anomalies, Foreign Object Debris (FOD), assembly errors and misalignments, and critical tolerance violations, ensuring that quality issues are caught before they can impact downstream processes or final product quality.
2. Comprehensive Measurement Traceability and Documentation Solutions
Vision Engineering’s measurement systems deliver complete traceability capabilities that address AS9100’s stringent documentation requirements.
Documentation and Measurement Features
The easy-to-use measurement software exports reports in multiple formats for documentation and streamlined NCR processes, reducing administrative burden while ensuring compliance. Programmable, automated and repeatable measurement routines ensure consistency across all operators, eliminating variability that can compromise quality standards. Digital archiving of all measurement data creates permanent audit trails that satisfy regulatory requirements. Automated report generation reduces documentation time while improving accuracy, allowing quality teams to maintain productivity without sacrificing compliance.
Key traceability benefits include exportable inspection reports meeting audit requirements, complete digital documentation of measurement data, repeatable and programmable measurements for consistent quality assurance, and simplified calibration tracking and documentation that reduces administrative overhead.
3. Ergonomic Design for Human Reliability
Vision Engineering’s eyepiece-less design philosophy directly addresses human factor challenges that can compromise inspection quality and operator wellbeing.
Ergonomic Benefits
Our inspection systems reduce operator fatigue during extended inspection cycles, maintaining inspection accuracy throughout long shifts. Natural body positioning improves accuracy through enhanced comfort, allowing operators to maintain focus on quality rather than physical discomfort. The elimination of repetitive strain injuries common with traditional microscopes protects workforce health and reduces absenteeism. Increased inspector productivity and consistency result from improved ergonomics, while intuitive operation reduces training time and operator errors, accelerating workforce development.
First Article Inspection (FAI)
These advanced inspection systems provide complete dimensional verification with traceable documentation, ensuring all FAI requirements are met. Surface finish assessment meets aerospace standards through high-resolution imaging capabilities. Automated report generation streamlines FAI requirements, reducing the time needed to complete first article documentation while maintaining accuracy and compliance.
In-Process Quality Control
Real-time defect detection prevents downstream issues by catching problems at the source. Statistical process control data collection enables trend analysis and continuous improvement. Immediate feedback enables rapid process adjustment, minimizing scrap and rework while maintaining quality standards.
Final Inspection and Verification
Pre-shipment quality assurance with full documentation ensures products meet all customer requirements before delivery. Custom inspection protocols can be developed for specific customer requirements, ensuring flexibility while maintaining standardization.
FOD Control Programs
Our systems enable detection of microscopic foreign particles that could compromise product performance. Cleanliness verification with image documentation provides objective evidence of FOD control effectiveness. Complete audit trails for FOD prevention protocols demonstrate compliance with aerospace cleanliness standards.
Demonstrated Results
Aerospace manufacturers implementing Vision Engineering solutions report significant improvements in AS9100 compliance metrics. Reduced rework through early defect detection saves time and materials while improving delivery performance. Audit performance improves through comprehensive documentation that satisfies even the most demanding auditors. Scrap reduction via accurate first-time inspection reduces material waste and associated costs. Customer confidence enhances reputation through consistent quality delivery, leading to increased business opportunities.
Technical Specifications Summary
System | Application | Key AS9100 Benefit |
---|---|---|
Lynx EVO | Visual inspection when magnification over 15x is required with camera option | 3D visualization for complex geometries |
Mantis PIXO | Detailed inspection with fixed magnification up to 15x with camera option | High-resolution surface analysis |
EVO Cam Series | Real-time digital inspection | Image capture for immediate defect identification and reporting |
Swift PRO Series | Combines video and optical non-contact measurement in a robust yet compact system | Fast, traceable measurement with minimal operator influence |
LVC Series | Fully automated 3-axis measurement systems with optional touch probe | Automated inspection of larger aerospace components |
TVM Series | Instant measurement of any component shape with place-and measure functionality | Traceable dimensional verification |
Deltron | High precision CMM for complex components with automation features | Repeatable, programmable inspection |
Conclusion
AS9100 compliance presents significant challenges that extend beyond procedural requirements. Manufacturers need technological solutions that address the real pain points of defect detection, measurement traceability, and human reliability. Vision Engineering’s inspection and measurement systems provide aerospace and defense manufacturers with proven tools to overcome these challenges while improving operational efficiency and reducing quality-related costs.
By investing in Vision Engineering technology, manufacturers not only meet AS9100 requirements but build a foundation for sustainable competitive advantage in this demanding industry.
Next Steps
To evaluate how Vision Engineering solutions can address your specific AS9100 compliance challenges, contact us for an application assessment or to schedule a system demonstration.